Telecommunication Business
Telecommunications and broadcasting networks form the foundation of the information society. DKK provides support with cutting edge technology and abundant experience.
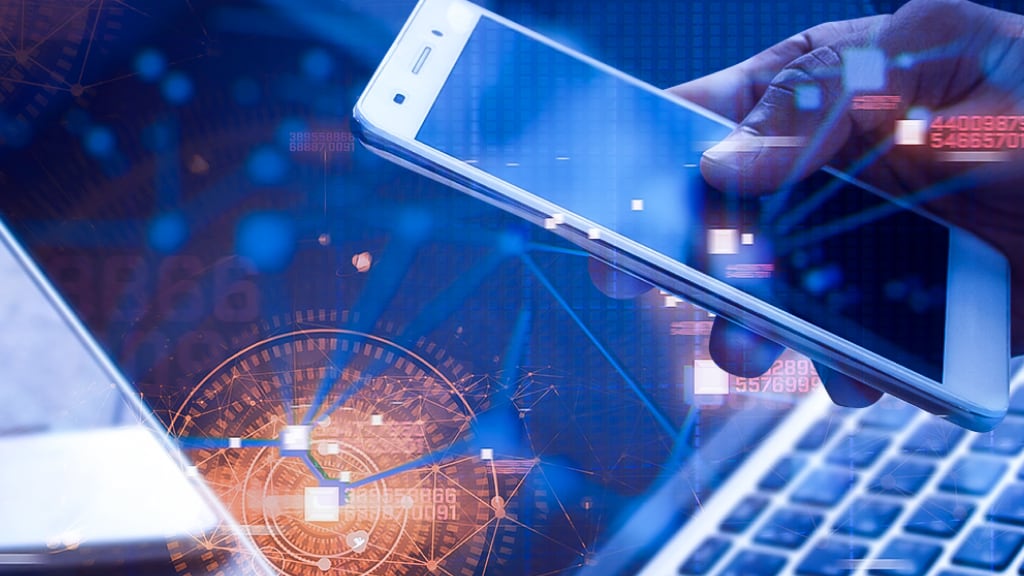
Induction Heating Business
DKK’s clean and efficient induction heating energy is used widely in industry, especially in the automobile industry.

News Release
View All News ReleaseIR News
View All IR News
Sustainability
We are promoting group-wide efforts to realize a sustainable society.